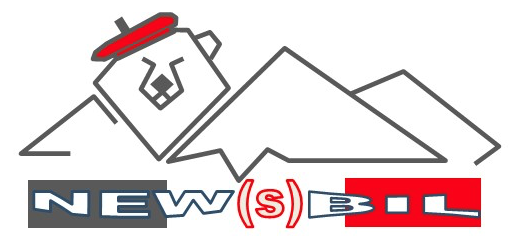
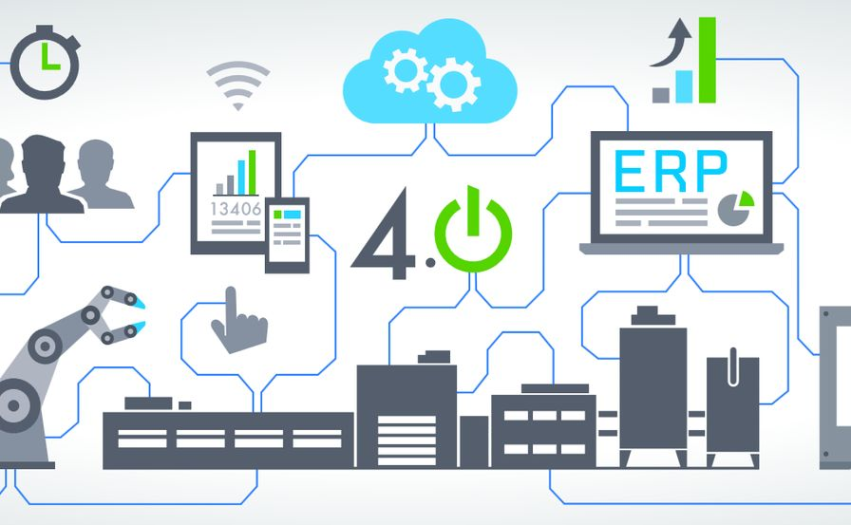
L'Usine du Futur : une réalité d'auhjourd'hui
Le contexte d’une 4ème révolution industrielle. Replaçons-nous un instant dans le contexte de l’industrie et de son évolution. Nul n’est sans savoir aujourd’hui que l’industrie a subi plusieurs révolutions industrielles :
- ère révolution au 18ème siècle : l’arrivée du charbon et de la machine à vapeur permettant la production mécanique.
- ème révolution au 19ème siècle : la production de masse grâce à l’arrivée de l’électricité.
- ème révolution au milieu du 20ème siècle : la production automatisée grâce à l’arrivée des automates et des robots.
Nous vivons aujourd’hui une 4ème révolution industrielle basée sur le rapprochement des usines avec le monde de l’Internet au sens large. Cette révolution est très souvent appelée “Industrie 4.0”.
Pourquoi le rapprochement entre Internet et les usines ?
Tout simplement parce que les technologies digitales, Internet et les usages du numérique que nous connaissons dans notre vie privée arrivent maintenant dans le monde professionnel. Pour parler de ce phénomène incontournable du 21ème siècle, nous parlons de “transformation numérique ou digitale“.
Les technologies clés pour l’usine du futur
- La réalité augmentée : technologie permettant, grâce à de lunettes numériques, de visualiser des éléments et informations numériques en « surcharge » de la réalité. L’intérêt est par exemple de guider un opérateur de maintenance lors des opérations effectuées sur une machine, ou bien encore d’accompagner des collaborateurs dans des processus d’apprentissage.
- La fabrication additive : technologie aujourd’hui relativement démocratisée permettant de réaliser dans des temps records, et avec de plus en plus de précision, des pièces en simplifiant tout le processus de fabrication. Son application est directe pour des prototypes de validation ou pour des pièces de rechanges ou de maintenance.
- L’internet des objets (aussi appelé IOT ou objets connectés) : technologie embarquée sur des pièces ou sur des machines pour effectuer des relevés d’information en temps réel, afin de pouvoir analyser leurs comportements. Les objets connectés sont par exemple de plus en plus utilisés pour suivre en temps réel les cadences d’utilisation des machines, afin de prévoir les opérations de maintenance (réaliser de la maintenance prédictive et minimiser ainsi les taux d’arrêt des machines et outils de production).
- Le Big Data : technologie purement numérique ayant pour but d’analyser d’énormes volumes de données dans des temps de plus en plus courts. Le Big Data prend tout son sens avec les objets connectés. En effet, plus les relevés de mesures sont fréquents et importants, plus les données sont précises et plus les actions pourront être efficaces. Mais cela entraîne des volumes d’informations collectées importants qu’il faut être capable d’analyser rapidement.
- Le Cloud computing : technologie déjà très répandue et utilisée dans la gestion des logiciels et des données. Elle apporte des avantages évidents sur la suppression des infrastructures lourdes dans les entreprises, sur la suppression des opérations de mises à jour et de maintenance, etc…
- La simulation : technologie souvent basée sur la modalisation 3D, elle permet de bénéficier du numérique pour simuler des comportements. Elle permet aussi bien de mesurer la résistance d’une pièce ou d’une machine dans son fonctionnement avant même qu’elle ne soit conçue, que de tester et vérifier une ligne de production et les cadences de fabrication.
- La cybersécurité : technologie directement induite de l’arrivée du numérique, elle a pour objectif d’assurer la sécurité et l’intégrité de l’ensemble des données qui peuvent transiter sur les différents systèmes. On pense tout de suite aux objets connectés avec le transfert des données mesurées vers les serveurs de stockage et de calcul, ou bien encore aux données et instructions utilisées pour piloter les automates et robots d’une chaîne de fabrication afin de conserver le plein contrôle des actions effectuées.
Nous comprenons très bien que ces différentes technologies vont apporter de réels gains au sein d’une entreprise, chacune dans un domaine ou sur un sujet particulier, permettant ainsi d’améliorer le système productif. Et l’usine connectée dans tout ça ?
L’usine du futur est une usine connectée qui dialogue
L’interconnexion de toutes ces nouvelles technologiques liées au numérique.
Va permettre de mettre en place un « système de dialogue » entre les outils et postes de travail. Ceux-ci vont donc pouvoir échanger des informations entre eux, mais aussi avec l’extérieur, et ainsi être encore plus efficaces en tenant compte de leur environnement.
Va permettre d’optimiser l’outil de production, et de répondre ainsi à des enjeux incontournables pour les industriels :
- Produire plus rapidement
- À meilleur coût
- Avec une agilité plus importante
Des gains et des leviers de performance incontestables
Dans ce contexte, l’entreprise industrielle devient donc une “usine connectée”, apportant ainsi des gains évidents
- Une plus grande flexibilité pour répondre aux variations dans les demandes clients (volumes, types de produits…)
- Une traçabilité plus poussée, pour réagir plus vite en cas de dysfonctionnement
- Une réactivité et une adaptabilité plus importantes, avec des machines capables de déclencher un appel de support, ou d’être pilotées à distance pour améliorer leur fonctionnement
- Une optimisation des cycles de production, grâce à la simulation numérique de l’organisation de la fabrication en fonction de la demande client pour la personnalisation d’un produit
Un suivi et un pilotage global de l’usine via un ordonnancement exemplaire
Pour maîtriser les délais de livraison, réponse aux modifications de commandes clients, coupler ressources et production complexe… les industriels ont besoin d’une solution d’aide à la décision pour optimiser la production. L’ordonnancement et la planification repose sur la prise de décision et la comparaison de scénarios tels que : nouvelle commande client, panne machine, retard approvisionnements, problème qualité, maintenance préventive etc… En appui d’un ERP, une solution de planification et d’ordonnancement à capacité finie permettra :
- Fiabilisation des délais de livraison client
- Une amélioration de la productivité homme et machine
- Une réduction des stocks (en cours, matières approvisionnées et produits finis) ainsi du temps de cycle
- Un gain de visibilité sur l’ensemble de la supply chain (logistique, production, achats, approvisionnements, vente)
- Pérennité et unicité d’une solution collaborative de planification et d’ordonnancement
Elle doit s’ouvrir sur l’ensemble de l’écosystème de l’entreprise, en intégrant les acteurs extérieurs tels que les clients, partenaires, fournisseurs, etc…. C’est plutôt « un écosystème connecté » que « une usine connectée »…
Aucun commentaire
Vous devez être connecté pour laisser un commentaire. Connectez-vous.